Transforming Materials Technology!
Electric vehicles (EVs) are getting a lot of attention these days, but many people may feel that their adoption is slower than expected. Why is that?
There are likely to be a number of reasons behind the spread of electric vehicles (EVs), including a lack of charging infrastructure, long charging times, and short driving ranges. Battery weight and longevity, as well as vehicle prices, also seem to be hindering adoption.
The importance of weight reduction:
These factors vary, but weight reduction is an important issue as it relates directly to range and cost.
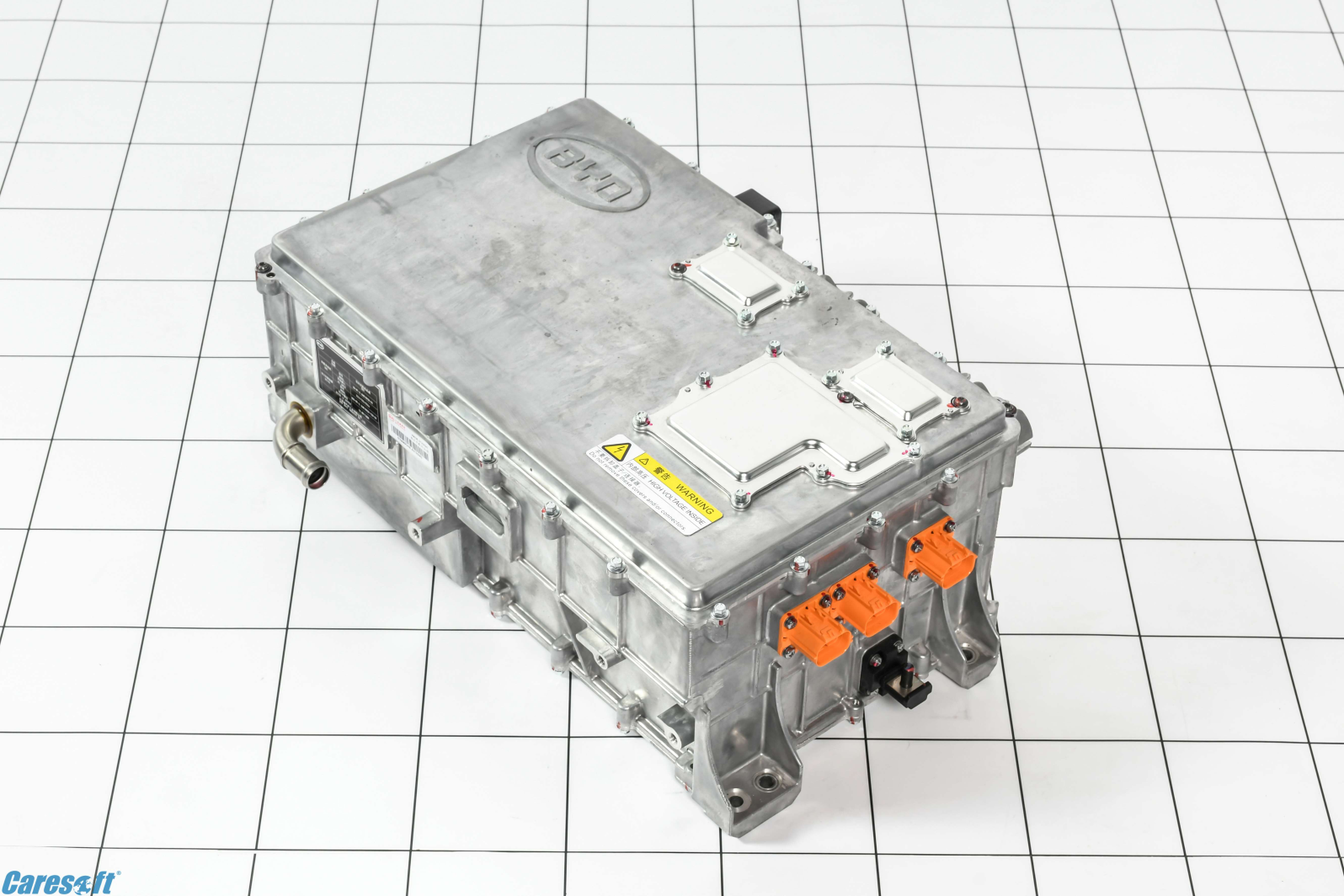
All Rights Reserved.
Metals have excellent thermal conductivity, efficiently release heat from heating components such as electric motors, and prevent equipment from overheating. Metals are also strong and protect equipment when used as enclosures. They are also highly durable and less susceptible to external influences. In electric vehicles (EVs) equipped with electronic equipment, aluminum (Al) alloy castings are commonly used.
New possibilities with material conversion:
In previous gasoline vehicles, the engines operated at extremely high temperatures, making it unsuitable to use resin components. In electric vehicles, however, the required heat-resistant temperature has decreased, and resin with insulating properties has become more popular. As a result, the use of resin parts has increased even in regions where metal products were traditionally abundant. Metal Substitution with Resin By switching to resin, the mass is significantly lighter than that of metal products. In addition, the color and shape can be easily changed, processing is easy, and the degree of design freedom is increased. However, resin is inferior to metal in heat dissipation and electromagnetic shielding. High temperatures and electromagnetic waves can cause malfunctions and poor performance of electronic components. Therefore, our company has developed resin moldings that offer both heat dissipation and electromagnetic shielding, and aims to reduce weight by replacing metals.
Find more information:
Our company is combining technologies (1) Injection molding with thermal-conductive and EMC shielding,、②Thermal-conductive greases CGW R series、and (3) 3D Thermal Gap pad, to propose the use of heat-dissipating resin for the housing of key components in electric vehicles, such as the OBC (on-board charger), inverter case, and ECU case which are often considered the heart of electric vehicles. For more information, please refer to our proposal.
Frequently Asked Questions (FAQ)
- Q:How much lighter is it than aluminum die cast?
- A:Achieving a weight reduction of 45%, our heat dissipation and electromagnetic shielding resin molding surpasses aluminum die casting.
- Q:Are heat dissipation and electromagnetic shielding functions applied by coating or plating methods?
- A:We use our proprietary material technology to apply heat dissipation and electromagnetic shielding functions directly to molding resin itself.