Film-in-mold Technology


-Challenge- Improved mirror visibility and safety
While most rear-view mirrors have glass surfaces, the shards can injure passengers in the case of an accident. In addition, conventional mirrors have blind spots, leaving the driver unable to see many parts around the vehicle. However, adding mirrors to prevent this may block the view of the road.
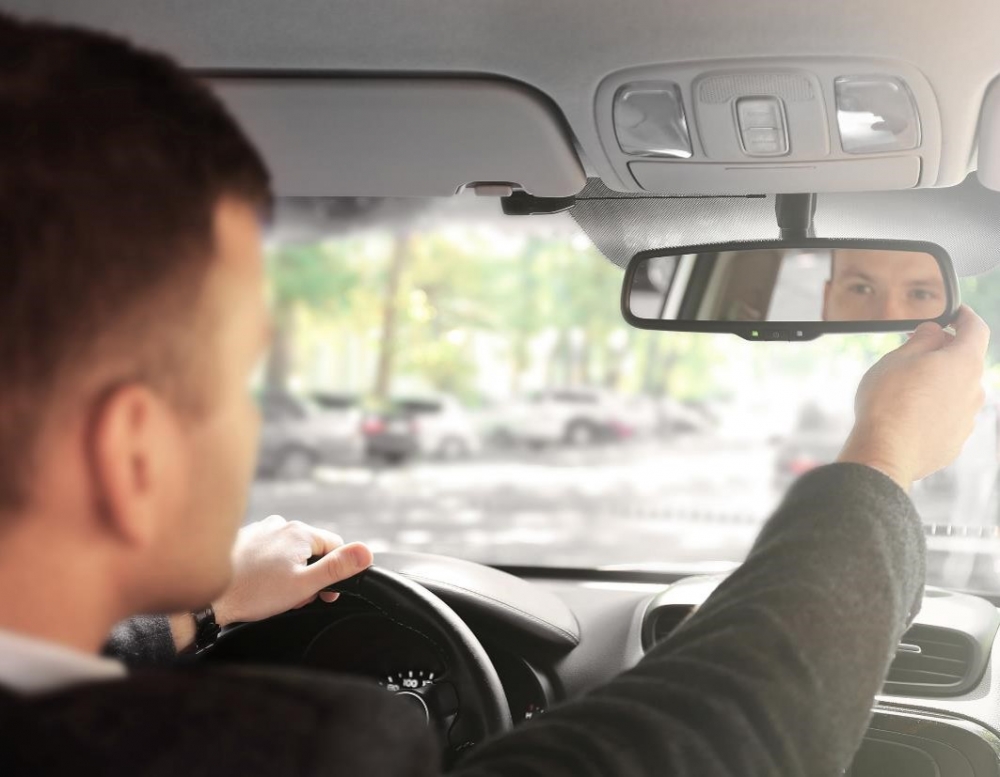
-Solution- Plasticization to accommodate curved surfaces and prevent cracking
With SEKISUI’s film-in-mold technology, we offer a molding method in which a film foil with a pre-printed design or pattern is placed between two injection molds, filled with resin, and then transferred onto the surface of the product using heat and pressure. High-brightness and high-reflectivity aluminum vapor deposited foil with a hard coat layer improve the elongation and cracking of curved surfaces. In addition, since decoration can be applied at the same time as molding, the need for decoration in secondary processing is no longer necessary, making this method able to reduce costs by reducing the number of processes.
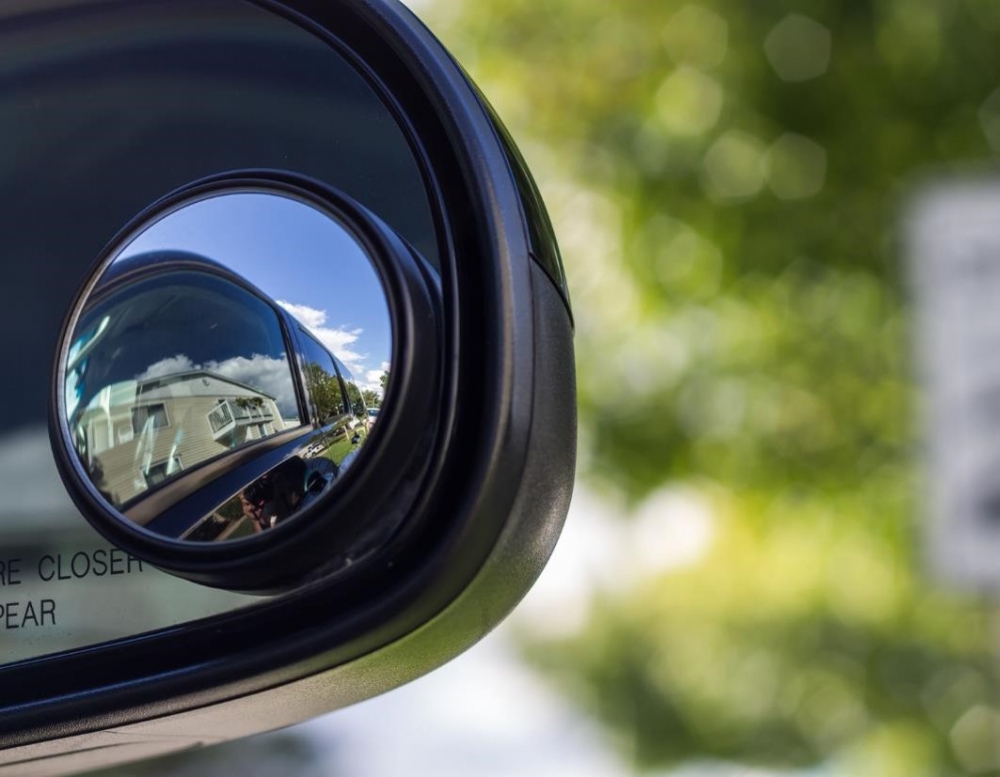
-Technology- Technical information
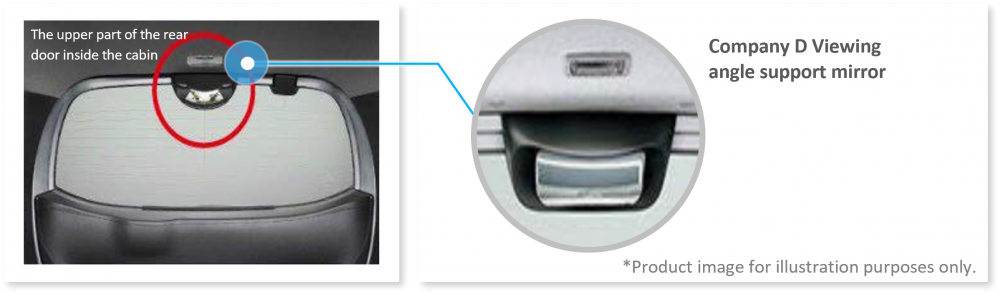
Technical overview
All-purpose resin to film In-mold injection
Mold injection (electric motors)
Molding and decoration are done simultaneouslyby first feeding the film into the mold,
then adhering the transfer film onto the injected resin.
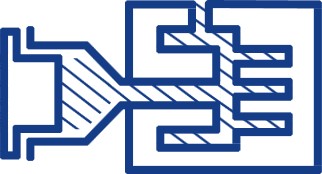
Film selection suitable for shaping into product
Highly luminate and reflective aluminum
evaporation foil with hard coat layer
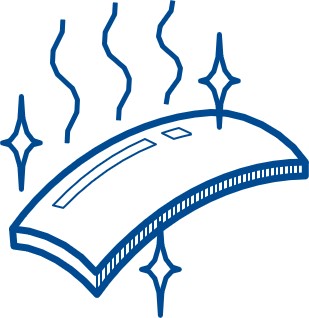
Improved performance and
added value compared to plating
Improved performance/value
- High reflectivity
- Reduction of environmental impact
- Lightweight
- Stretch Crack (Whitening) Prevention Product/Mold Design
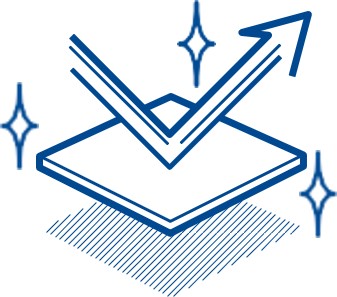
Versatile application
Automobile interior parts
- Conversation mirror
- Visual aid mirror
- Interior ornaments(As decorative items)
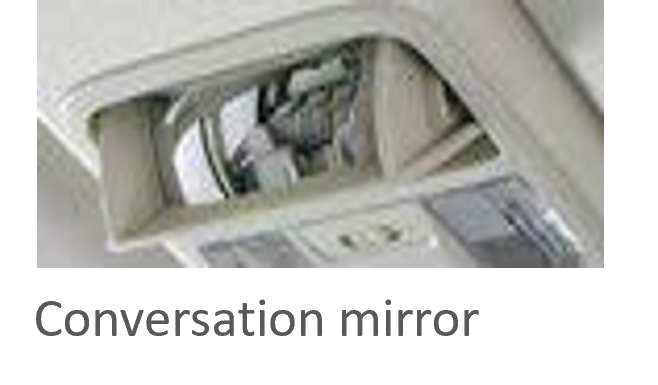
Technical details
Molding process : In-mold
Servo-balance design technology
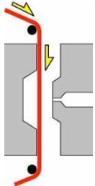
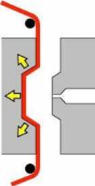
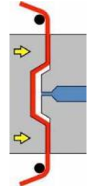
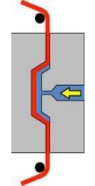
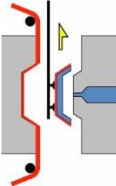
adhered to the mold
Film composition
Film composition optimization

High curvature products
Improved stretch cracking
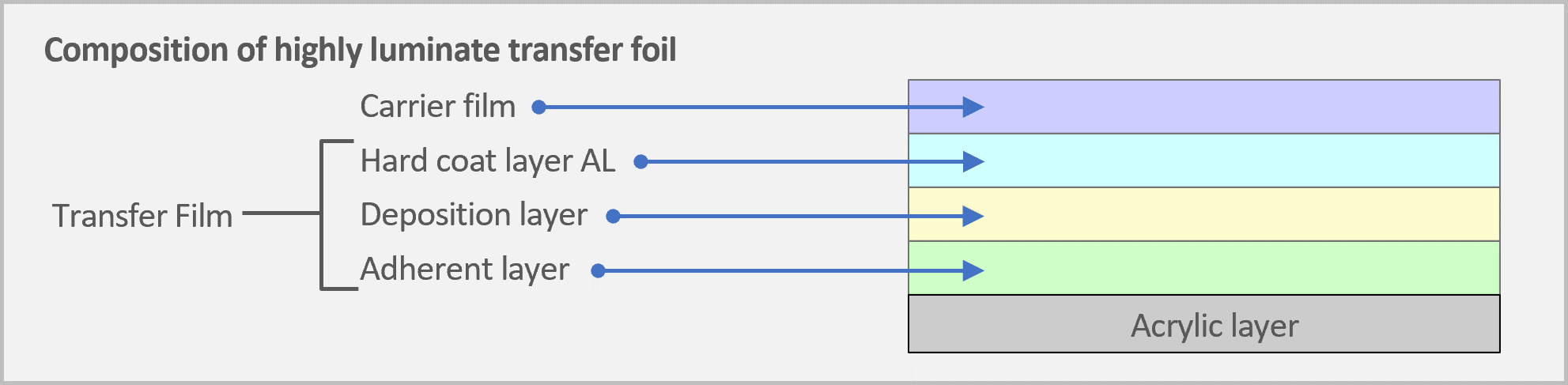
Performance/effectiveness comparison :
Comparison with resin mirror
Item | Plating | Aluminum foil IMD | Performance Evaluation/Effectiveness | |
---|---|---|---|---|
Value | Cost (including amortization) | 10 | 9 | Cost reduction of approx. 10% (estimation) by a single process *Differences in reduction rates occur depending on the shape |
Weight reduction | △ | ○ | Weight reduction Approx. 15% | |
Reflectanc | △ | ○ | 85% reflectance, 20% improvement over chrome | |
Environmental burden | × | ○ | Non-Hexavalent Chromium | |
Safety | △ | ○ | No metal layer (plating) peeling | |
Shaping (curvature) | ○ | △ | Can be shaped about the size of the viewing angle support mirror |

- Benefits
- ・ Free design with transfer foil
- ・ Functional layers can be added to the transfer foil (hard coat, metallic, corrosion resistant, etc.)
- ・ Unlike decorative film insert molding, no trimming of the excess film is required
- ・ Cost reduction by a single processes